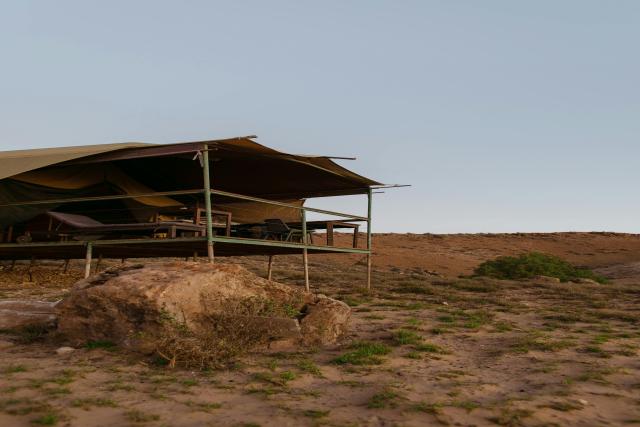
If you're thinking about getting a new storage facility, warehouse, or even a temporary sports complex, then fabric buildings might be an excellent option for you. These structures strike the perfect balance between affordability, durability, and versatility. But how much exactly will a fabric building set you back?
Unlike traditional brick-and-mortar buildings, fabric structures are highly customizable. This means the total cost can vary depending on several factors. This article will guide you through the elements that impact fabric building costs, helping you make the best decisions when budgeting for your project.
Building Size
Size is probably the most influential factor in fabric building cost. It's simple math: the more square footage you need, the more materials and construction effort are required. This applies to both the footprint area and the height-taller buildings demand stronger support structures to keep everything stable and upright.
But here's the cool part-fabric buildings are inherently efficient. Because they utilize clear-span designs with minimal interior columns, you can maximize usable space within the building's footprint. This can be a major advantage compared to traditional buildings, where support beams can eat into valuable floor space.
Design Complexity
Imagine the difference between a basic white t-shirt and a designer gown with intricate embroidery. The same principle applies to fabric buildings. Simple rectangular fabric structures with a standard peak roof will be the most cost-effective option.
As you introduce design complexities like curves, multiple rooflines, or significant variations in height, the price will start to climb. This is because these features require more specialized planning and fabrication of the fabric cover and its supporting structures.
At the end of the day, total functionality and longevity are the elements that should matter. Thus, engineered fabric buildings created by industry experts are your best bet. These structures boast durability even in the most extreme of environments, thanks to high-quality materials that make them up.
Fabric Choices
The fabric itself is a key component of the building, and the type you choose will impact fabric building costs. There is a wide variety of materials available, each with its own strengths and weaknesses. These choices include:
Polyethylene (PE)
A cost-effective option, PE fabric is lightweight and well-suited for temporary structures or storage in mild climates.
Polyvinyl Chloride (PVC)
Offering greater strength and durability than PE, PVC fabric is a good choice for permanent structures and those in harsher weather conditions.
Beyond the base fabric, you may also consider additional features like insulation or fire-retardant coatings. These features will enhance the functionality and safety of your building but will come at an added cost.
Foundation
Just like any structure, a fabric building needs a solid foundation to make sure it's stable enough to withstand many external elements. The type of foundation required will depend on the size and intended use of the building.
For smaller, temporary structures, a simple gravel base or concrete pad might suffice. However, larger permanent buildings will require a more substantial foundation system, such as piers or footings.
The specific soil conditions on your building site will also help determine the foundation requirements.
Consulting with a professional engineer is crucial for ensuring a safe and secure foundation for your fabric building.
Customization
The basic shell of the fabric building is just one piece of the puzzle. Of course, you would want to include features like doors, windows, or skylights to enhance functionality and accessibility. The number and type of these add-ons will impact construction costs.
For example, a large roll-up door for easy equipment access will be more expensive than a standard pedestrian door. Similarly, heavy-duty fire doors will add more to the price than basic access doors.
Installation Considerations
While some fabric buildings are designed for self-assembly, hiring a professional installation crew is often recommended. Experienced installers can ensure the building is erected correctly and meets all safety standards.
This is especially important for larger or more complex structures. The cost of installation will vary depending on the size and complexity of the building, as well as the experience level of the crew.
Long-Term Value
While upfront cost is certainly a major consideration, it's important to remember that fabric buildings offer excellent long-term value.
Here are some additional factors that could also affect fabric building cost:
Energy Efficiency
Tension fabric buildings can be designed to be energy-efficient, particularly when incorporating insulated fabrics and skylights. This can lead to significant savings on HVAC system costs over time.
Low Maintenance
Fabric buildings typically require minimal maintenance compared to traditional buildings. The fabric cover is resistant to rot and mildew, and the supporting structures are built with durable, low-maintenance materials.
Relocation Flexibility
Every project has unique needs. So, if these needs change down the line, some fabric structures can be disassembled and relocated to a new site. This inherent flexibility can be a valuable asset for businesses with uncertain futures.
By combining affordability with energy efficiency, low maintenance requirements, and potential relocation flexibility, fabric buildings offer a smart and cost-effective solution for the long term.
In Conclusion
Fabric buildings bring something unique to the table as an alternative to traditional construction methods. By getting familiar with the key cost influences outlined in this article, you can go into the construction planning and purchasing process as a savvy customer.
But remember, the most cost-effective option isn't always just the cheapest sticker price. So, seek out a flexible fabric building that checks every box while being able to adapt as your requirements evolve down the road. With some careful planning alongside a reputable supplier, your fabric structure can be an amazing long-term asset giving you massive cost savings.