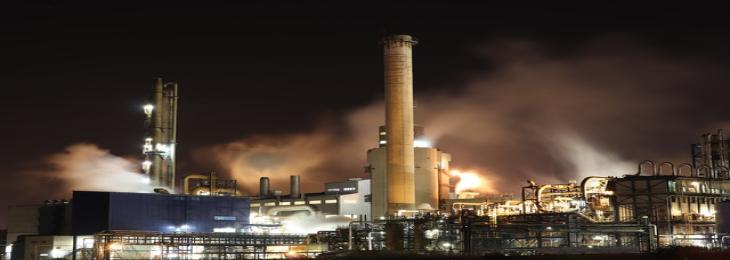
A new variant of refractory alloys is being developed to increase the engine efficiency of aircraft and gain control over the emission of CO₂ in the environment.
Recently, researchers from the University of Miami, have initiated research that may reduce the emission of heat-trapping gas from aircraft. Assistant professor James Coakley from the College of Engineering in Miami is trying to design a new generation of high-temperature alloys. These alloys are refractory minerals that are very much heatproof.
According to a study conducted by International Council on Clean Transportation in 2019, all commercial air travel emitted a total of 918 million metric tons of CO₂. The passenger aircraft cover 85% of that CO₂ emitted. However, extreme heat levels can endanger the current batch of alloys used in the manufacturing of engines, lowering their power and stability up until the breakdown.
Aerospace engineers have depended on alloys using nickel-based materials for a long time to build turbine blades, disc-plates, and other important aircraft turbine elements. While refractory elements like tantalum and tungsten are recognized for their resistance to corrosion and heat, they happen to be overweight, putting unneeded pressure on aircraft engine components. Therefore, blending various elements like tough tungsten among lightweight titanium, for creating a different kind of refractory alloy with various characteristics.
Lately, the research team led by professor Coakley decided to conduct some study cases on an experiential alloy in Tennessee. With the incorporation of automatic filling among a furnace to duplicate situations inside a turbojet engine, the research team subjected the alloy to high temperatures, also extra tension to different periods. Simultaneously, the team also watched the new alloys using neutron beams to determine their deformability. The goal of this experiment was to reach higher toleration to pressures and temperatures. The results of these tests are still being examined.
This project will become a large achievement for the efforts in reducing the carbon footprint of the aeronautical industry. The manufacturing of this alloy for the jet turbine will affect the carbon footprint left by air travel. This will help to restructure the imbalance of hazardous gases in the environment.